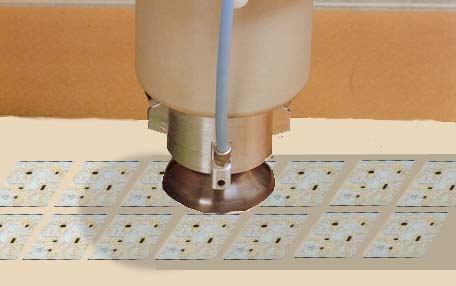
The charging of the line can be
effected by hand or automatically. The substrates are laid on the transport
belt. As transport means paper or foil can be used. The substrate is
transported from the entry through the spraying booth to the exit.
Within the spraying booth the
substrates are coated with ink which is atomized by a rapidly rotary bell and
charged with high voltage.
The distance between the
atomizing bell and the substrate can be continously adjusted by motor.
A continiously adjustable gear
pump supplies the high speed rotary bell directly from the ink drum. In case
that several ink have to be held available, each of them is provided with a
pump and a branch hose to the atomizer. In this way changes from one ink to
another can be effected in a few seconds by a short flush of the bell.
Also conductive ink can be
sprayed because of the special design. Near the exit after having left the
spray booth the boards are transported through a flash-off zone where highly
volatile solvents evaporate.
Air is cleaned with finest filter
before entering the spray booth.
The spray cabine is under light
pressure to prevent outer influences like dust etc. from entering. Possibly
escaping solvent
emissions are sucked off in the
entry and exit zones to prevent spoiling solvent emissions from entering the
cabine and disturbing the operation staff's work.
The air from the inside of the booth is sucked out
via filtering mats fixed on both sides of the transport belt within the
booth. |